陶瓷基板散热技术
陶瓷基板采用Al₂O₃材质,热导率>200W/(m・K),适用于IGBT模块散热。金属化工艺采用DPC(直接敷铜)技术,铜层厚度35-200μm,附着力>5N/cm。表面可涂覆导热硅脂(热阻0.5℃・cm²/W),与散热器紧密贴合。结构设计:铜层图案采用叉指型散热通道,增加表面积30%。对于双面散热,可设计通孔阵列(直径1mm,间距3mm),提升散热效率。测试数据:某IGBT模块使用陶瓷基板,结温从125℃降至85℃,功率密度提升40%。成本分析:陶瓷基板成本约为FR4的5-10倍,但长期可靠性提升明显,适合高功率应用。 18. DFM 分析需包含 SMT 贴装性评估,推荐使用 DFMEA 工具。广州打样PCB类型
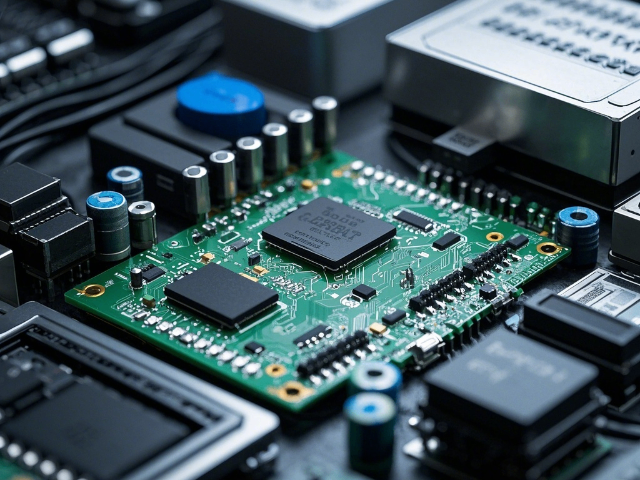
云平台协同设计与知识产权保护
云平台协同设计支持多人实时编辑,自动检测。设计文件通过区块链存证,确保知识产权保护,版本追溯精度达分钟级。支持Gerber、BOM等文件在线预览,无需本地安装设计工具。技术架构:①分布式版本控制(Git);②权限分级管理;③数据加密传输(AES-256)。客户价值:某设计公司通过云平台,异地协作效率提升50%,设计文件泄露风险降低90%。商业模型:按用户数或项目收费,提供基础版(5用户)、专业版(20用户)等套餐。 中山最小孔径PCB设计服务6. Altium Designer 支持 Gerber 文件智能导入,自动识别阻焊层与丝印层。
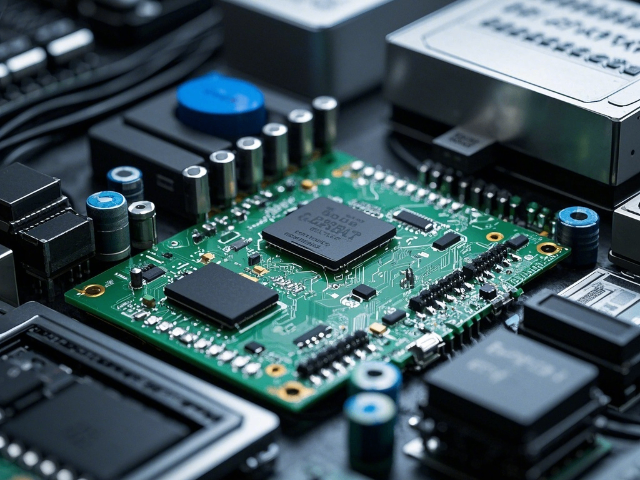
DFM分析与可制造性设计
DFM分析需包含SMT贴装性评估,推荐使用ValorNPI工具。重点检查BGA焊盘设计(如0.5mm间距焊盘直径0.3mm)、测试点覆盖率(>95%)、元件布局密度(≤80%)等关键指标。对于0201元件,焊盘间距需≥0.15mm,确保贴片机吸取精度。优化策略:①添加工艺边(3mm宽度);②设置Mark点(直径1mm,间距50mm);③分散高热元件布局,避免局部温度过高。效益数据:某企业通过DFM优化,SMT贴装良率从97.2%提升至99.5%,生产效率提高25%。典型案例:某路由器主板通过DFM分析,发现0.4mm间距BGA焊盘设计缺陷,修正后良率提升4%,节省成本超50万元。
未来PCB技术挑战与机遇
未来PCB面临的挑战包括:更高集成度(如Chiplet)、更低功耗(如量子计算)、更严格环保要求(如可降解材料)。机遇在于新能源汽车、AI服务器、6G通信等新兴领域的需求增长。企业需加大研发投入,布局先进封装、智能生产等技术。战略建议:①建立联合实验室开发前沿技术;②引入AI优化设计与生产;③构建绿色供应链体系。市场洞察:据Yole数据,2025年先进封装基板市场规模将达200亿美元,年复合增长率15%。风险提示:技术迭代加速,需关注行业标准更新与客户需求变化。 37. 喷锡与沉银工艺在存储寿命上相差 6 个月,沉银更适合长期保存。
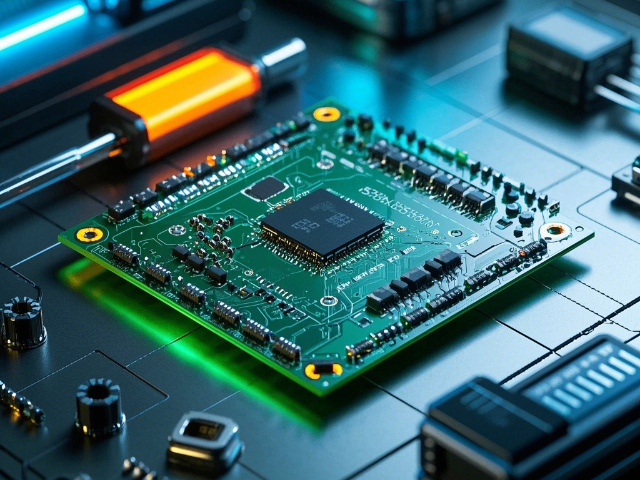
航空航天PCB可靠性设计
航空航天PCB通过MIL-PRF-31032认证,耐温-55℃~260℃。采用铝基复合材料,热膨胀系数与芯片匹配,减少热应力失效。表面处理采用化学镀镍金,厚度≥0.05μm,抗腐蚀性能达500小时盐雾测试。工艺要求:①通孔铜厚≥35μm;②镀层孔隙率<1个/cm²;③标识采用激光打标,耐温>300℃。应用案例:某卫星电路板使用该设计,在太空环境中稳定运行10年以上。测试标准:通过NASA标准测试,包括辐射、真空、微陨石冲击等。 绿色制造工艺推荐使用水性阻焊油墨,VOC 排放降低 80%。广州打样PCB类型
41. 绿油起泡常见原因:层压前未充分预烘或曝光能量不足。广州打样PCB类型
穿戴设备PCB防护技术
穿戴设备PCB采用纳米涂层技术,防护等级达IP68。盐雾测试>1000小时无腐蚀,满足汗液、雨水等复杂环境需求。涂层材料为聚对二甲苯(Parylene),厚度5-10μm,透氧率<0.1cm³・mm/(m²・day・atm)。工艺步骤:①真空沉积(温度150℃,压力10⁻³mbar);②等离子体处理增强附着力;③厚度均匀性检测。测试数据:某智能手表PCB通过该处理,在50℃、95%湿度环境中存储1000小时无失效。成本控制:纳米涂层成本约5元/片,适合高穿戴设备。 广州打样PCB类型
文章来源地址: http://dzyqj.m.chanpin818.com/pcbdlb/deta_26550152.html
免责声明: 本页面所展现的信息及其他相关推荐信息,均来源于其对应的用户,本网对此不承担任何保证责任。如涉及作品内容、 版权和其他问题,请及时与本网联系,我们将核实后进行删除,本网站对此声明具有最终解释权。